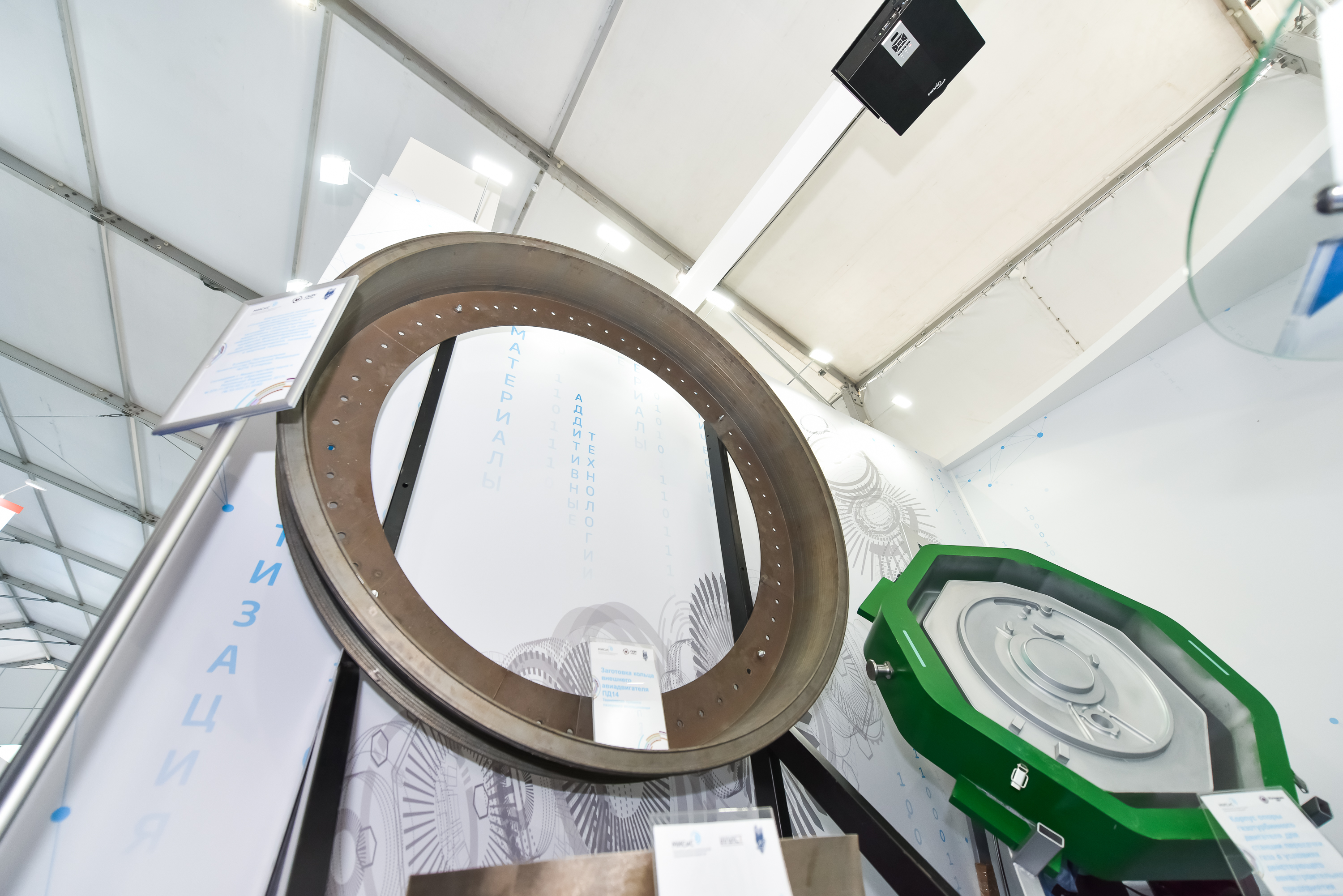
Создание конкурентоспособных авиационных двигателей невозможно без использования в их конструкции материалов и технологий нового поколения. Ученые СПбГМТУ и НИТУ «МИСиС» предложили использовать технологию прямого лазерного выращивания для создания внешнего кольца двигателя ПД-14. Первый экспериментальный образец заготовки был изготовлен в СПбГМТУ с использованием уникального оборудования собственной разработки.
«Прямое лазерное выращивание — аддитивная технология, которая позволяет значительно повысить эффективность производственного процесса. Например, корпус камеры сгорания для небольшого газотурбинного двигателя можно вырастить с нуля за 3 часа, в то время как при использовании традиционных технологий на изготовление уйдет около двух недель. В нашем случае для создания заготовки детали потребовалось около 130 часов, при том, что габариты заготовки составляют более 2-х метров в диаметре. Масса заготовки уменьшилась более чем втрое. Это значит, что кардинально снижается объем последующей мехобработки, соответственно, сокращаются сроки изготовления, снижается производственная себестоимость, обеспечивая тем самым конкурентоспособность отечественных авиационных двигателей», — отметил один из разработчиков проекта, директор института ЭкоТех НИТУ «МИСиС» Андрей Травянов.

Для создания внешнего кольца двигателя ПД-14 был использован титановый сплав, который в виде порошка газовой струей подавался под лазерный луч, оплавляющий его, обеспечивая послойный «рост» детали. В результате инженеры миновали стадии отливки, ковки и раскатки заготовки. Процесс производства ускорился на порядок, при этом механические свойства выращенного материала не уступают изделиям металлопроката и значительно превосходят свойства литых изделий, что подтверждено результатами механических испытаний, проведенных как в лабораториях НИТУ «МИСиС», так и в независимых лабораториях, включая Центральную заводскую лабораторию (ЦЗЛ).
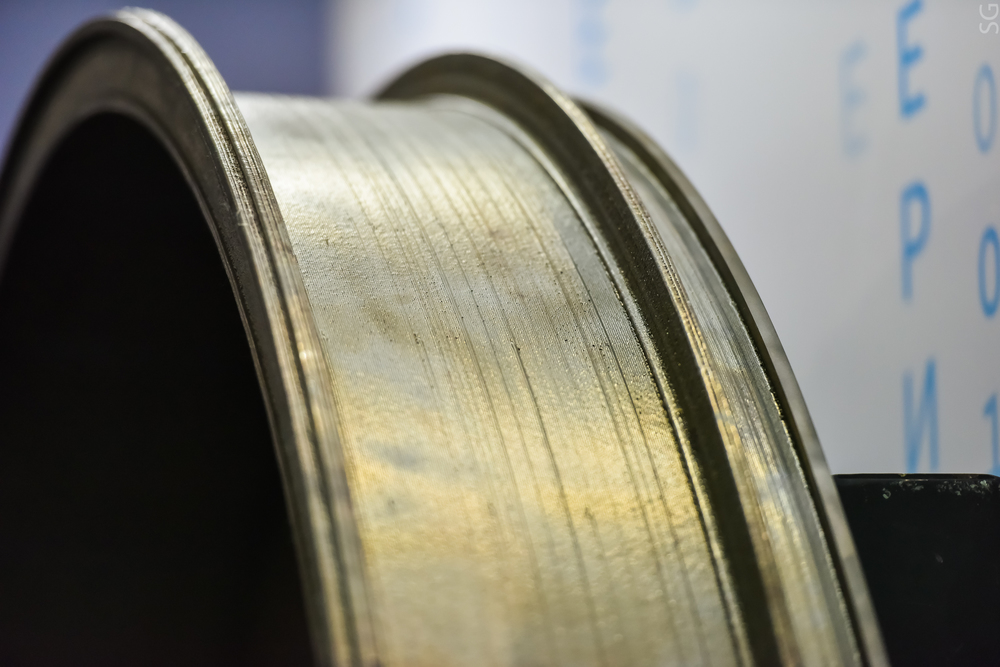
Еще одно технологическое преимущество использования аддитивных технологий при создании авиадеталей — конструктор видит результаты в режиме реального времени, и может быстро вносить необходимые изменения. Процесс проектирования и создания новой техники с использованием данного метода ускоряется в десятки раз. Технология дает возможность комбинации нескольких газопорошковых струй и подачи различных материалов в зону выращивания, создавая тем самым изделия с градиентными свойствами, то есть одна часть детали может быть коррозионностойкой, а другая — жаростойкой, что особенно важно для аэрокосмической отрасли.
«Изготовлению этого образца предшествовали всесторонние теоретические и экспериментальные исследования: были разработаны математические модели процесса, проведено большое количество металлографических исследований, томографии и рентгенографии образцов, механических испытаний, определены оптимальные режимы и стратегии выращивания, изготовлено несколько макетов.В ходе выращивания опытного образца было применено несколько новых технических решений, которые в настоящее время находятся в стадии правовой защиты. Например, выращивание горизонтальным лазерным лучом, использование „динамической“ подложки для борьбы с образованием трещин, технологические приёмы увеличения производительности процесса, прогнозирование термических деформаций и их учет в технологической модели изделия при генерации управляющей программы для обеспечения требуемой точности построения», — подчеркивает ответственный исполнитель проекта, зам. директора по научной и проектной деятельности Института лазерных и сварочных технологий СПбГМТУ Евгений Земляков.
В настоящее время готовятся испытания полученного узла двигателя на базе одного из ведущих профильных двигателестроительных предприятий России. Начало промышленного производства запланировано на 2020 год. Полученный положительный опыт позволит также использовать разработанные технологии и при проектировании и изготовлении двигателя ПД-35.
Комментарии (43)
Shpakov
10.10.2019 10:09Хм… на сайте МИСиС эта новость появилась еще 2 сентября. Мне кажется, спустя месяц можно было бы и более развернутую статью сделать — например, раскрыть момент с новыми техническими решениями да и акцент может быть стоило сделать не на «Впервые в мире» (в чем, как я вижу, уже возникли сомнения), а на более важном моменте, в тексте упомянутом вскользь: "разработаны математические модели процесса, проведено большое количество исследований… определены оптимальные режимы и стратегии выращивания".
Потому что можно конечно, купить готовое изделие и «не парится» (имею в виду камеру для «выращивания»), но гораздо круче разобраться самим в теории процесса. Пользы от этого гораздо больше, чем от простого копирования имеющейся технологии, пусть даже и с некоторыми улучшениями — странно, если бы их не было, прогресс всетаки на месте не стоит.
Еще для полноты картины можно было бы добавить сравнение с существующими процессами/изготовителями — в чём они уступают, ограничения существующих технологий (почему не смогут сделать такое же изделие с теми же параметрами) и т. д. В общем, хочется подробностей.vad_nes Автор
10.10.2019 11:15Спасибо вам большое. Хорошее предложение, мы подумаем — может, и сделаем такую статью. Там и товарищ ниже хорошие советы дает.
ghrb
10.10.2019 10:54+1был изготовлен в СПбГМТУ с использованием уникального оборудования собственной разработки
Вот это бы поподробнее раскрыть. А то в подобных новостях всегда ожидается что-то вроде «мы купили принтер и напечатали». А если здесь создан прототип собственного принтера, то на мой взгляд это куда интереснее самой детали.vad_nes Автор
10.10.2019 11:18Спасибо большое. Я выше уже написал, подумаем, может и попробуем сделать статью не столько о конкретных достижениях, сколько про наши наработки в области аддитивных технологий. Просто университет сейчас очень серьезно это направление развивает, и там есть о чем поговорить.
NEIR0N
10.10.2019 11:51Может и технология хорошая и принтер хорош и результат хороший. Но в рамках того количества двигателей которое у нас производится совершенно скорее всего не выгодно. Внедрение технологии будет достаточно дорогое. И скорее всего в кб скажут, что технология слишком сложная и проще на коленке детальку спроектировать с худшими характеристиками. Еще интересно было бы увидеть насколько ухудшились механические свойства. Я думаю масса то снижена за счет оптимизации конструкции, а сам материал имеет более низкие механические характеристики. И такую же по массе деталь можно изготовить стандартными техпроцессами или я ошибаюсь?
Am0ralist
10.10.2019 11:55Еще интересно было бы увидеть насколько ухудшились механические свойства.
Хм…
Процесс производства ускорился на порядок, при этом механические свойства выращенного материала не уступают изделиям металлопроката и значительно превосходят свойства литых изделий, что подтверждено результатами механических испытаний, проведенных как в лабораториях НИТУ «МИСиС», так и в независимых лабораториях, включая Центральную заводскую лабораторию (ЦЗЛ).
NEIR0N
10.10.2019 13:16при этом механические свойства выращенного материала не уступают изделиям металлопроката. Звучит расплывчато....)
Klenov_s
10.10.2019 23:51Насколько я помню по практике на Салюте, эта деталь требует очень точной обработки, но несет не самые большие нагрузки.
А вобще да, очень удивительно как материал полученный методом не сильно отличающимся от литья может конкурировать с материалом, прошедшем обработку давлением?
Oleg_Dolbik
10.10.2019 13:11Внедрение технологии в данном случае — одно на целый ряд деталей. Тем более что именно при опытном производстве и малых объемах эта технология супер выгодна — для массового производства дешевле вложиться в линии, которые будут лить/штамповать/сваривать на автоматах.
NEIR0N
10.10.2019 13:29Вот и не так, одно дело корпусную деталь изготовить, а другое дело лопатку вентилятора или диск изготовить. Для каждой детали будет своя специфика расчета процесса выращивания. Это не так что научился кольцо выращивать и теперь можешь в двигателе любые кольца растить.
SvSh123
10.10.2019 17:15Вот как раз при небольших объемах такие технологии особенно выгодны. :)
NEIR0N
10.10.2019 17:43+1а в чем выгода то? оптимизировать по массе ту же деталь, и выпускать ее по старым технологиям. Стоит у тебя токарь и фрезеровщик, получают по 30к. Станки уже есть, делают они не только 1 деталь. А тут принтер купи, специалиста оплати и он еще 1 деталь в год делать будет. В чем выгода то? Это если с 0 производство сферическое в вакууме открывать, то там выгодно будет.
radonit
10.10.2019 18:46А ещё штамп сделай, пресс купи, сварку купи, найти сварщика (т.к скорее всего раньше из нескольких деталей делали), да ещё и брак появится при сварке.
С какого то момента да, старые технологии выгоднее, но не при малых партиях.
Только штамп может несколько миллионов стоить например.NEIR0N
11.10.2019 06:43Дак в том то и фикус что у старых технологий 0 вложения. Для пд-14 уже изготавливается данная деталь на старых технологиях уже имеющимися сотрудниками и ничего вкладывать не нужно. И делают там 3 двигателя в год. А тут новая технология которую внедрять надо и деньги тратить. При этом она не даст существенного конкурентного преимущества и как делалось 3 двигателя так и будет. Поэтому внедрение в старый техпроцесс новых технологий не выгодно на стадии производства для любых партий изделия. В этом есть смысл при разработке нового изделия. к примеру как написано пд-35. только смысла производить 2 убыточных двигателя нет.
radonit
11.10.2019 07:38Деталь может быть сборкой, состоять из нескольких частей, что повышает процент брака, особо если части свариваются/парится. Штампы и литиевая оснастка изнашивается и требует замены, что стоит денег. Ещё больше проблем при необходимости внесении изменений в документацию.
Тут же универсальная технология, сначала корпус, завтра та же установка лопатки делает, послезавтра форсунки.
Но в целом верно, заменять в лоб старую деталь новой, при том что старая уже в серии и имеет всю оснастка нерационально, а вот если параллельно упрощается конструкция/меняется число технологических операций — другое дело.
Wijey
11.10.2019 08:54Почему не даёт то? Написано же
Например, корпус камеры сгорания для небольшого газотурбинного двигателя можно вырастить с нуля за 3 часа, в то время как при использовании традиционных технологий на изготовление уйдет около двух недель.
Получается уже не 3 двигателя в год, а гораздо больше можно делать, если и другие детали изготавливать тем же способом.
cyberly
10.10.2019 21:56Ну, станки не могут делать детали абсолютно любой формы. Инструмент должен как-то подлезть к обрабатываемой поверхности. Например, невозможно выточить закрытую внутреннюю полость в монолитной детали.
Klenov_s
10.10.2019 23:54Для этой детали не требуются внутренние полости, зато требуется последующая обточка на координатно-расточном станке.
Foreglance
10.10.2019 12:03В этом видео (по английски) популярно рассказано какие «ещё» операции (постобработки) приходится производить над аддитивной печатью металлом (а также о точности изготовления изделий) — из той части информации, что обычно стараются избегать на промо-презентациях:
youtu.be/nyYcomX7Lus
kababok
10.10.2019 13:09Ых, тогда вот вопросы:
Какие и чьи электропривода были использованы в установке? (речь в первую очередь об инвертерах векторного/серво-управления и "верхних" контроллерах CNC-процесса).
Какие программные пакеты используются для моделирования?
А какие — для управления установкой?
Какие типы управления используются в установке (каскадное регулирование, управление с наблюдателями, количество осей свободы и т.п.)?
Чем и как производится охлаждение цели в технологическом процессе (точечное/по всему объёму/динамическое/константное и т.д.)?
Интересно ведь! :))))
gromazeka
10.10.2019 14:06-1Зря старались, закроют вас как непригодных и ещ е20 прилагательных, кто же это в здравом уме будет терять кормушки на отливку, ковку, прокат и т.п. металлов, там такие деньжища завязаны, а ваша скорость и вес, да кому они нужны, ну может получите пару заказов от кого нибудь на детали для какой нибудь ангары, которые в итоге забракуют…
Во общем ждите смены тренда лет так через 200 )
lowtechomega
10.10.2019 18:47Лазерное спекание это, а не выращивание — давно уже все спекают. А так заинтересовал заголовок, думал что новое чего придумано. Про впервые в мире… 2 метра… что то большие сомнения.
dzsysop
10.10.2019 20:56Ну с одной стороны да, лазерные принтеры тоже какой-то порошок «спекают».
Я не специалист, но наблюдая за успехами 3D печати, я обнаружил что это целый новый мир. И в зависимости от того что именно и как мы «спекаем» меняется очень многое. Кто-то цемент спекает и дома строит. Кто-то мясо печатает. В основном народ конечно разными пластикамипечатаетспекает.
Насколько я понимаю печать металлами она конечно уже есть, но распространение пока очень узкое и специфичное. Поэтому мне кажется вполне возможным что спекание специальных (или даже уникальных) сплавов при помощи таких же уникальных лазеров, вполне может быть очень инновационным и «первым в мире».
И если у вас есть сомнения, попробуйте их как-то обосновать.
trir
не верю habr.com/ru/company/smile-expo/blog/379573
vad_nes Автор
В вашей заметке:
У нас:
trir
ну так это заметка 2015, может они с тех пор и больше печтают — просто не кричат об этом на весь мир
vad_nes Автор
Ну, если это вопрос веры и «а может быть» — не смею препятствовать верить дальше, что «чумазый не может». )))
trir
www.sciaky.com/additive-manufacturing/industrial-metal-3d-printers
EBAM 300
Размеры камеры 300” (7620 mm) x 108” (2743 mm) x 132” (3353 mm)
ну и чем вы хвастаетесь?
vad_nes Автор
Вы правда не понимаете разницы между «у нас есть 3D-принтер с большой камерой» и «мы изготовили крупногабаритный узел авиационного двигателя»?
trir
А вы их спрашивали?
robo-hunter.com/news/3d-pechat-v-aviastroenii-rasskaz-injenera-boeing13552 © robo-hunter.comvad_nes Автор
Если вы обратили внимание, мы даже в заголовке специально акцентировали внимание на слове «крупногабаритный». Эти корпуса для турбин, как видно из этого снимка, сложно назвать крупногабаритными —
Это первое. Второе — одно дело распечатать корпус турбины, другое — функциональный узел двигателя. Требования к качеству деталей несколько разнятся.
trir
на вашей первой фотке деталь не сильно больше или это другая деталь?
akaAzazello
Пока не пройдена сертификация этой детали в двигателе, рано говорить о том, что у вас крупногабаритная авиационная деталь, а не тестовый образец ;)
vad_nes Автор
Поправка принимается. )
SvSh123
Вообще-то это другая технология. Единственный в мире производитель таких принтеров Optomec на данный момент предлагает принтеры с рабочей зоной не больше кубометра. Так что да, это впервые в мире.
Можете и дальше гордиться достижениями США, мы их нисколько не умаляем. :)
trir
а в статье об этом ни слова
SvSh123
Во что?
Что это создано у нас? Или что оно в принципе существует? :)
trir
что впервые в мире